Our Policy and Strategy
Given that toys are primarily played with by children, we need to do our utmost to ensure product safety. To that aim, necessary toy-related safety conditions are determined based on the national requirements of individual countries and voluntary toy-industry standards. However, we note that these conditions are becoming increasingly complex and diverse due to differences in individual cultural, social, and other environments. Furthermore, the growing diversification of toys that accompanies technological progress and social change is further complicating the application of necessary safety-related conditions. While the overall aim is to provide safe toys, we sometimes cannot guarantee safety simply by conforming with national and industry requirements and so we use our past experience and expertise to evaluate and investigate any elements that are not covered in the existing requirements and strive to formulate ever safer toy-making processes.
In accordance with our founding philosophy, the TOMY Group commits to a fundamental quality policy that creates environment-conscious products which people can play with comfortably and confidently and offers good-quality toys that are attractive to customers worldwide. The TOMY Group has formulated internal product safety and quality management rules that systemize the relevant flow across the entire toy-making process from planning through manufacture, and TOMY Group product quality rules relating to product safety and chemical substances.
Management Structure
●Safety & Quality Assurance Group
The Safety & Quality Assurance Group, under the direct control of our representative director and president, is responsible for managing TOMY Group product safety, quality, and chemical substances. In terms of quality assurance, the Group compiles product quality documents based on the TOMY Group product quality rules, confirms product quality at every stage of the manufacturing process, and strives to guarantee full compliance with all product safety and quality standards. To ensure product safety, the Group takes all safety considerations into account before commercializing a product to avoid any accidents. In the rare event that an accident does occur, they set up a Risk Management Task Force headed by our president in accordance with our recall rules to plan and implement product recalls, investigate the cause of the accident, and prevent a recurrence.
●Safety & Quality Liaison Meeting
The Safety & Quality Assurance Group holds regular safety and quality liaison meetings, made up primarily of TOMY and Group companies in Japan. The meetings share product-related information, as well as propose and implement initiatives to improve product quality and safety.
●Safety Leader System, Concentrated Play Sessions
Each year, different units within the TOMY Group, including Group companies inside and outside Japan and our development, sales, quality control and customer service departments, assign one safety leader to further strengthen awareness of the importance of safety and product quality. Each safety leader fulfills that role for a fixed period of one year, and new safety leaders are assigned every year. We aim to instill a strong awareness of safety across the entire Group by ensuring many employees serve as safety leaders. Throughout the year, safety leaders work to increase safety awareness in their own departments and participate in Concentrated Play sessions with the aim of pinpointing and ultimately improving any potential safety issues that could possibly happen during play. We have a system in place to immediately implement appropriate improvements in the rare event of a problem being discovered during the play activity.
Key Initiatives
Product Safety and Quality Management
The TOMY Group strives to ensure safety and preempt any problems by compiling product safety and quality management rules and systemizing their relevant flow across the entire toy-making process from planning through manufacture. Regarding product safety, in particular, the TOMY Group conducts investigations based on our own unique product quality rules, which are stricter than the toy-industry safety standards represented by the Safety Toy mark, to suit global product deployment. Many different customers use toys, but we need to pay particular attention to ensuring safety standards for children that are tailored to suit specific growth stages. To achieve that, each safety standard laid out in the TOMY Group product quality rules differs depending on the age group they cover, and is set to reduce foreseen risks.
Major existing toy-related safety standards are listed below. The TOMY Group product quality rules conform to all of these standards.
Japan Food Sanitation Law
ST / Japan Safety Toy Standard
CPSIA / Consumer Product Safety Improvement Act
FHSA / Federal Hazardous Substances Act
ASTM F963 / American Society for Testing and Materials
Directive 2009/48/EC: Toys Safety Directive
EN71: European toy Regulations
SOR/2011-17: Canada Toys Regulations
GB 6675: National Safety Technical Code For Toys
ISO 8124: International Standard -Safety of toys -)
Please note that there are other regulations in addition to those listed above.
We have thorough safety and quality management systems in place across our entire toy-making process from planning through retail, including design reviews (DR) conducted at each development stage by production technology and product safety and quality personnel, final approval prior to mass production, shipping inspections and acceptance testing. We conduct these tests on all new products and sample inspections of regular existing products. In addition, we confirm the safety of manufactured products by conducting inspections of specific chemical substances, either with each order or over a set manufacturing period.
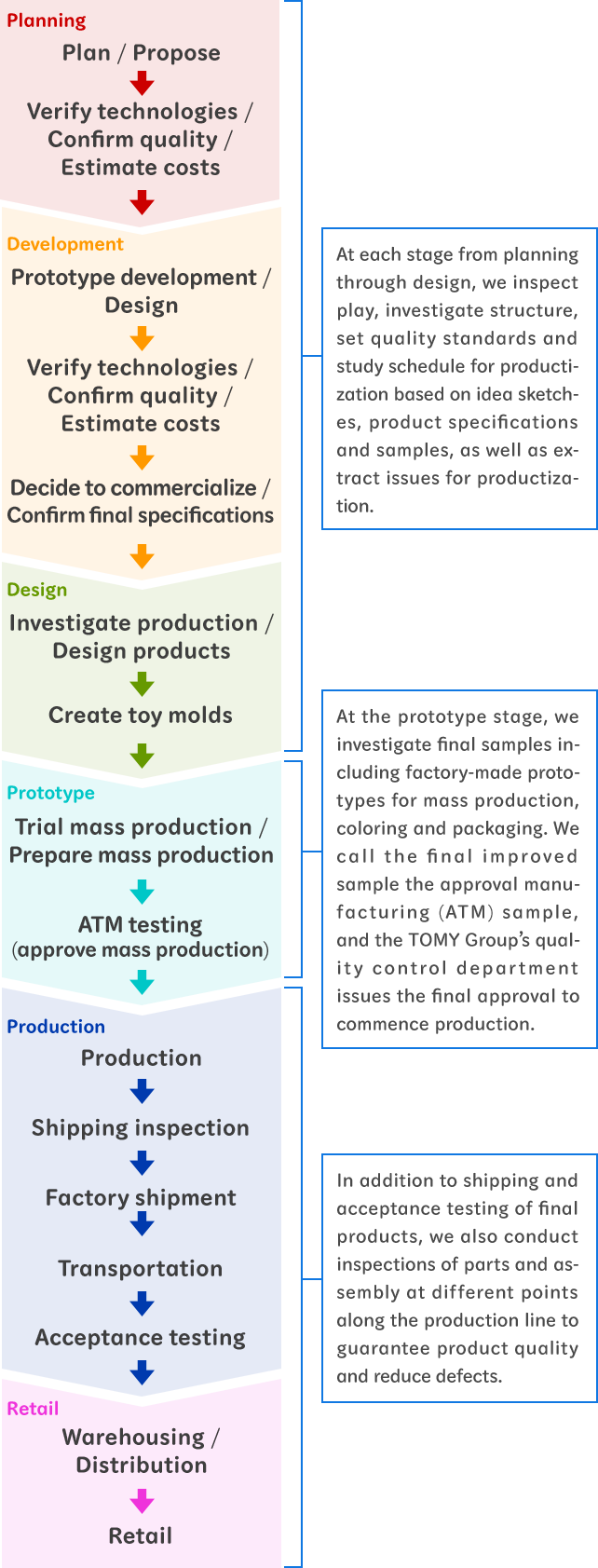
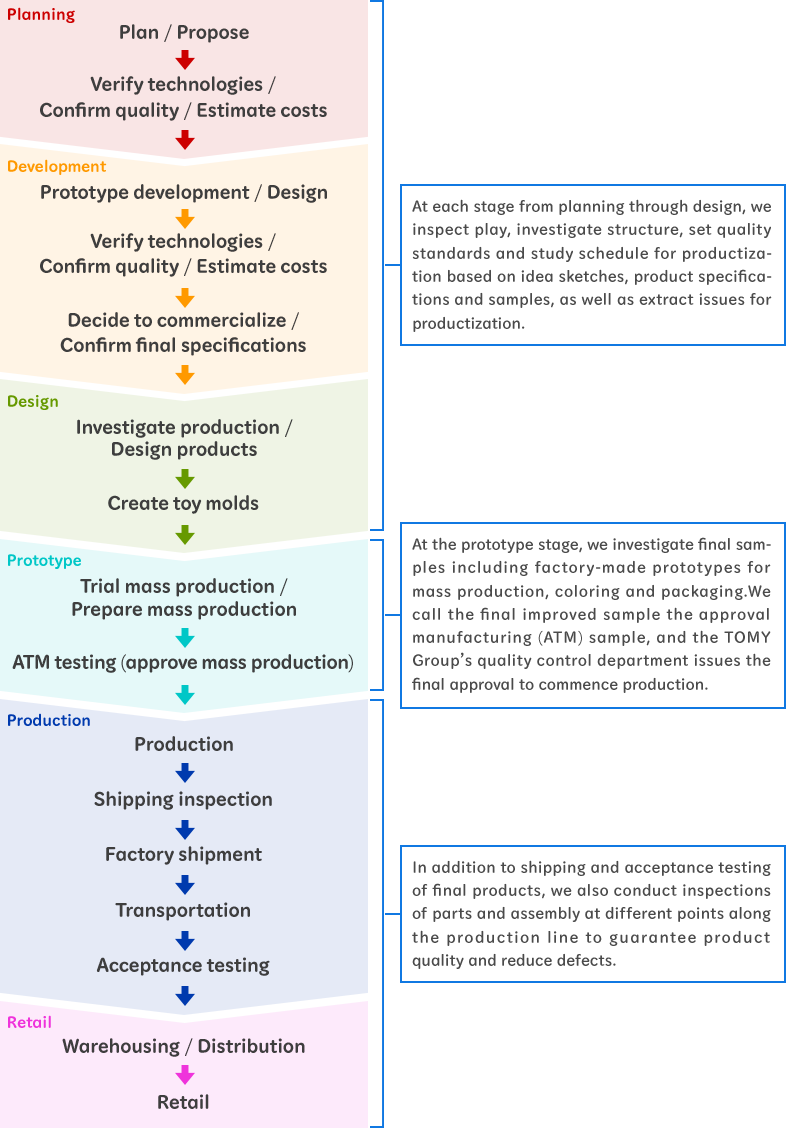
Toy safety considerations evolve as new toys and new technologies emerge, so we are repeatedly updating our TOMY Group product quality rules and analysis testing to stay abreast of those developments. We published the 2020 TOMY Group product quality rules in September 2019.
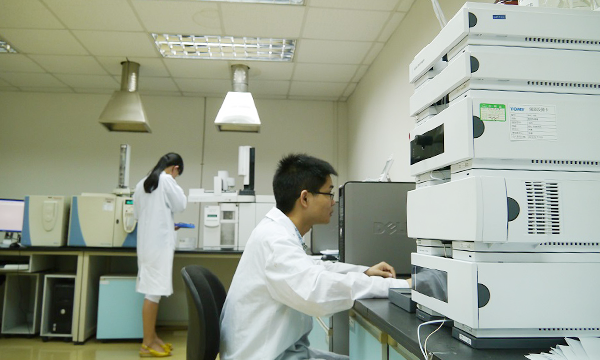
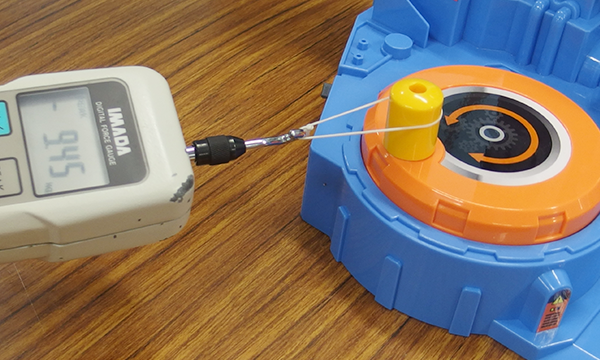
Furthermore, we focus on developing safety measures from a child’s perspective so that children can enjoy fun, safe play. That means displaying warnings and alerts on product packaging, in product instructions and on our company website that predict how a child might play with a certain toy.
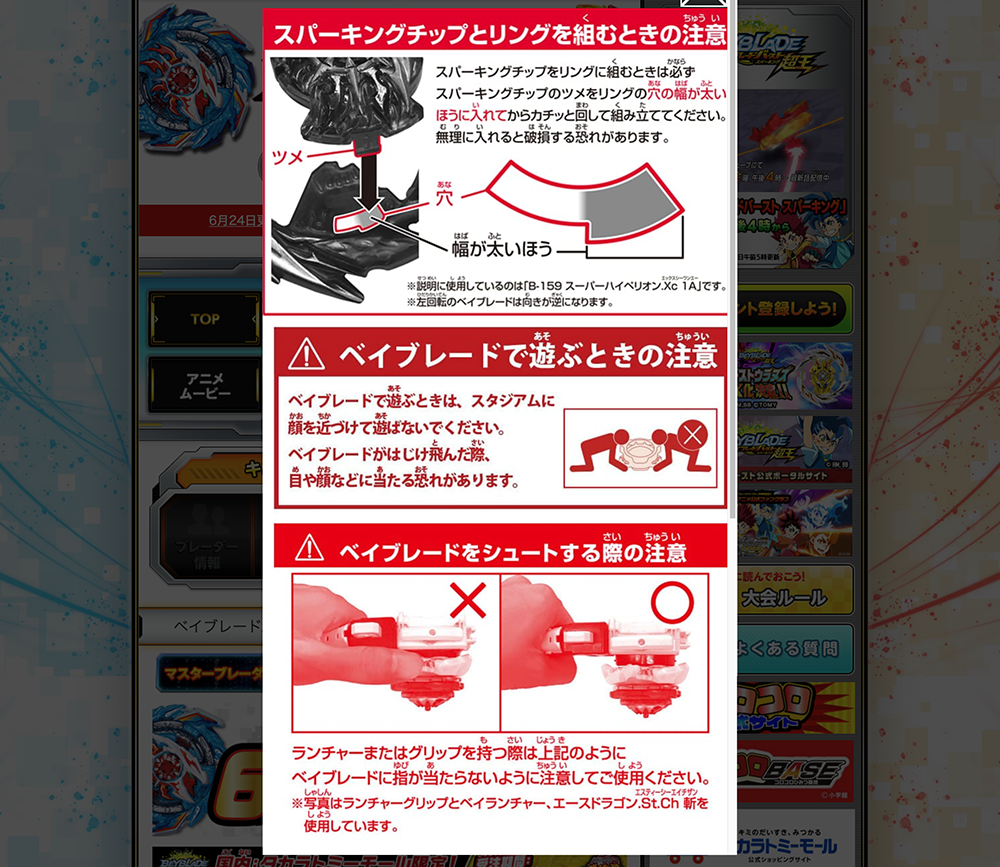
Chemicals Management
Toys consist of various different parts and materials, so we have to fully consider how a child’s health and environment might be impacted by chemical substances in toy parts and materials. Regulations surrounding manufactured goods and parts included in toys and electrical and electronic equipment differ from country to country, so we established TOMY Group Chemicals Management Policy and will strive to implement management of toxic chemical substances including during manufacturing.
TOMY Group Chemicals Management Policy(Established May 2022, Revised June 2024)
With TOMY Group’s ONE TOMY’s Promise to provide quality Asobi experiences to "fulfill the dreams of our stakeholders," the TOMY Group is committed, in its Code of Conduct, to "produce products that promote children’s healthy growth" and, in its Environmental Policy, to "protect our environment so that children can smile and continue to enjoy playing with toys." Since the Group's products, especially its toys, are targeted mainly at children, it is necessary to pay the utmost attention to the use of chemical substances to ensure their safety. It is also important to manage chemical substances properly and protect the global environment for the children of the future.
As technologies continue to advance, national standards and voluntary industry regulations have been implemented in many countries around the world, including Japan. In order to fulfill the TOMY Group’s Philosophies, the TOMY Group ensures proper management of chemical substances in accordance with the required standards. The TOMY Group also aims to eliminate as much as possible the use of chemical substances that may cause harm to the human body or the global environment across the entire value chain through measures such as replacement with low-risk substitute materials.
-
Scope of application
This policy applies to all manufacturing companies (business partners, factories and sub-contractors) involved in the manufacture of the TOMY Group's products.
-
Relevant standards
The TOMY Group complies with the laws, regulations, and international standards related to chemical substances in each country and region. In cases where the requirements differ according to the national laws of each country and internationally recognized standards, the Group aims to follow the higher standards as much as possible.
-
Managed areas and targets
This policy applies to chemical substances used in the TOMY Group's toy products. The TOMY Group also aims to improve upon this policy over time so that it can be applied beyond the current scope of application to include products other than toys and the entire production process.
-
Controlled chemicals
The TOMY Group manages the controlled chemicals specified in the TOMY Group product quality rules in accordance with this policy.
-
Management method
The TOMY Group demands that the manufacturers of the Group's products comply with the prohibition of banned substances at the time of manufacture, based on the relevant laws and regulations, and strives to implement management procedures in accordance with the TOMY Group Product Quality Rules.
In addition, the Group asks its suppliers to appropriately manage chemical substances across the entire organization in accordance with the TOMY Group Responsible Procurement Guidelines. It also requests that they conduct self-assessments of their management methods and other measures as needed and make improvements based on the results.
As an example of our management methods, we conduct testing in cooperation with third-party specialist organizations in order to detect and prevent contamination such as heavy metals or phthalate ester compounds in our products. Furthermore, in Europe we conduct chemical safety assessments (CSA) on our components and raw materials used in product manufacture. We monitor around 5,000 chemicals identified as carcinogenic, mutagenic, reprotoxic or otherwise harmful, and those of determined to be of very high concern, according to the RoHS Directive, the REACH Regulation, and the POPs Regulation.
In the future, we will expand this initiative beyond Europe to other regions. Even in the very unlikely event that a product does contain such contamination, we have mechanisms in place to prevent it from reaching our customers, and are working tirelessly to ensure consistent product safety and quality management.
List of TOMY Group priority regulated substances
List of TOMY Group priority regulated substances
Category | Examples of regulated substances |
---|---|
Heavy metals | Lead, Antimony, Arsenic, Mercury, Cadmium, Selenium, Barium, Chromium(Ⅲ, Ⅵ), Aluminum, Boron, Cobalt, Copper, Manganese, Nickel, Strontium, Tin, Organic tin, Zinc |
Phthalates | Bis-2-ethylhexvl Phthalate (DEHP/DOP), Butyl benzyl Phthalate (BBP), Di-n-butyl Phthalate (DBP), Di-iso-nonyl Phthalate (DINP) Di-iso decyl Phthalate (DIDP), Dioctyl Phthalate (DNOP), Di-n-hexyl Phthalate (DNHP/DHEXP), Di-isobutyl Phthalate (DIBP), Dicyclohexyl Phthalate (DCHP), Di-n-pentyl Phthalate (DPP/DPEP/DPENP), Diisooctyl Phthalate (DIOP) |
Flame Retardants | Halogenated flame retardants/non-polymeric organohalogen flame retardants include, but are not limited to, the following, Tris (1-chloro-2-propyl) phosphate (TCPP), Tris (1,3-dichloro-2-propyl) phosphate (TDCPP), Trio cresyl phosphate (TCP), Tris (2,3 dibromopropyl) phosphate (TDBPP), Tris (2-chloroethyl) phosphate (TCEP), Trisaziridinyl phosphinoxide (TEPA), Tetrabromobisphenol A (TBBPA), Bis(2-ethylhexyl) tetrabromophthalate (TBPH), Polybrominated diphenyl ether (PBDE), Polybrominated biphenyl (PBB), Polychlorinated biphenyls (PCB), Hexabromocyclododecane (HBCD), Short-Chain Chlorinated Paraffins (SCCP), 2,3,4,5-Tetrabromobenzoic acid, 2-ethylhexyl ester (TBB), Antimony trioxide, Tris-(2,3-dibromo-propyl)-isocyanurate (TBC), Decabromo-diphenyl-ethane, TBBA-(2,3-dibromo-propyl-ether), Bisphenol A diglycidyl ether, brominated, Brominated Epoxy Oligomers, Tetrabromobisphenol S Bis-(2,3-Dibromopropyl Ether) |
Azo Dyes | Biphenyl-4-ylAmine, Benzidine, 4-Chloro-o-toluidine, 2-Naphthylamine, o-Aminoazotoluene, 5-Nitro-o-toluidine, 4-Chloroaniline, 4-Methoxy-m-phenylenediamine, 4,4’-Diaminodiphenylmethane, 3,3’-Dichlorobenzidine, 3,3’-Dimethoxybenzidine, 3,3’-Dimethylbenzidine, 4,4’-Methylenedi-o-toluidine, 6-Methoxy-m-toluidine, 4,4’-Methylene-bis-(2-chloro-aniline), 4,4’-Oxydianiline, 4,4’-Thiodianiline, o-Toluidine, 4-Methyl-m-phenylenediamine, 2,4,5-Trimethylaniline, o-Anisidine, 4-Aminoazobenzene, 2,4-Xylidine, 2,6-Xylidine |
Others | Bisohenol A (BPA) Formaldehyde Boric acid Perfluroalkyl and Polyfluoroalkyl substances (PFAS) |
We also consider the environmental impact of incineration at the point of disposal, and have generally prohibited the use of polyvinyl chloride (PVC) packaging materials. We have also prohibited the use of materials that are highly likely to contain bisphenol A (BPA), such as polycarbonate in products that are likely to come into oral contact.
Policy for Managing Chemical Substances in Products
We promote the following initiatives to manage chemical substances in products.
1. Controlled chemical substances
We established the TOMY Group Product Restricted Substances List based on laws of various countries and regulations as well as internal standards, and we manage the chemical substances in our products in accordance with this list to ensure legal compliance and reduce environmental impact. This list will be revised as necessary in response to the expansion and revision of laws and regulations, the addition of voluntary standards, and other circumstances.
2. Production factory management through factory audits
We regularly conduct audits on product production factories based on our own auditing standards, and carry out production at factories that can appropriately manage the chemical substances in products.
3. Establishment of a management system for chemical substances in products
We promote both the introduction of a management system to identify and manage chemical substances in product parts and materials, as well as the management of chemical substances in products in cooperation with suppliers and production factories.
4. Chemical substance management including the supply chain
We promote the management of chemical substances in products and parts by using the TOMY Group product quality rules and the TOMY Group Product Restricted Substances List for suppliers and contracted manufacturers.
We also hold briefing sessions for suppliers to confirm their understanding and cooperation regarding the management of chemical substances in products.
Chemical substance management system
Request to suppliers/contracted manufacturers for survey and management of chemical substances used
Factory audits
Registration in system of information on chemical substances contained in products
Verification of chemical substance information; product inspection
Production
Final inspection
Shipment
Training and Awareness Building on Confidence, Safety, and Quality
Through various initiatives specified in our product safety and quality management rules, we seek to promote a shared awareness of safety across TOMY’s global operations. For example, we hold a Safety Day once a year where all Group employees worldwide jointly consider the importance of product safety, quality and control. This activity is designed to ensure adherence to safety standards issued by the toy industry in general and by individual countries, and promote ever safer toy manufacturing. We also hold Concentrated Play sessions roughly once a month where employees get together to play with actual toys from a customer’s perspective. We have a system in place to immediately implement appropriate improvements in the rare event of a problem being discovered during the play activity. Since their launch in 2009, these sessions have been expanded, with similar meetings currently being held across Group production companies in Japan, Thailand, Vietnam, and China.